Agroconnect greenhouse
The experiences will take place in the facilities that the Andalusian Institute for Research and Training Agrarian, Fisheries and Food (IFAPA), has in the Municipal District of the Cañada de San Urbano (Almería) at 36º50′ N and 2º24′ W and at a height of 3 meters above sea level.
An Almería-type greenhouse with a steel structure, polyethylene cover, east-west ridge orientation, and an area of 1,850 m2 is used. It has a central corridor 2 meters wide, from which secondary corridors with a width of one-meter branch off where the mobile robots navigate. It is divided into two sectors in which the following systems are available to action to control crop growth: natural ventilation (zenithal and lateral), heating and air cooling, enrichment systems CO2, humidifiers, dehumidifiers, system irrigation, and fertilization, and artificial led lighting. In order to monitor system variables and weather conditions inside and outside the greenhouse, there are six indoor stations IoT (Internet of Things) that allow measuring the temperature, relative humidity, environmental pressure, leaf wetness, solar radiation, PAR radiation, and CO2 concentration; or even terrain variables such as volumetric content, conductivity electrical and floor temperature.
There are also two outdoor weather stations that measure external variables such as precipitation, wind speed and direction, radiation, temperature and humidity, and CO2 concentration. At the level of measurement, control, and supervision, the greenhouse has its own cloud (fog), which in turn is incorporated into the cloud-based architecture (with the three layers Edge, Fog and Cloud) with the underlying idea of provider services, which integrates the rest of the systems that make up the facilities and that need to exchange information and orders between them: solar desalination, osmosis distillation, photovoltaic park, solar thermal installation, microalgae photobioreactors, etc; as well as external services such as weather forecasts, price information, etc.
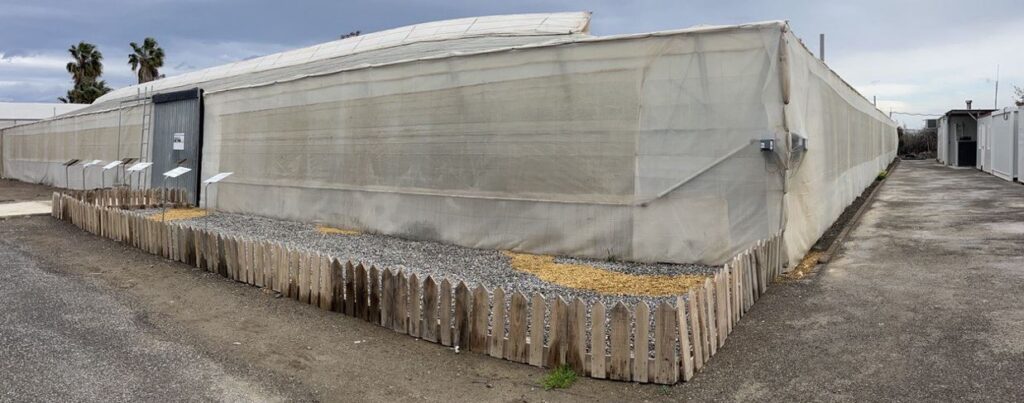
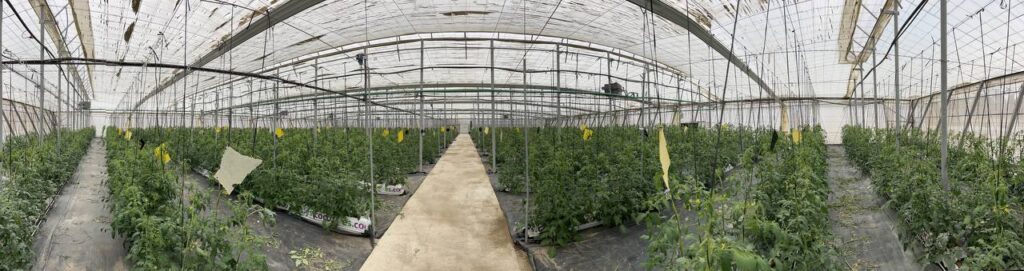
AgriCobIoT I
Description
The developed robot is based on the commercial platform Husky. It is a differential drive robot that allows zero-radius turns. This feature is essential for aisle change displacement in the greenhouse. The original structure of the robot is not adequate for transporting boxes, so it has been necessary to design an additional structure. This modification helps the farmer in harvesting and increases the usable area for the placement of all sensors and boxes. This structure consists of 4 central posts that raise it to a suitable height for the operator to deposit the vegetables. In addition, a removable implement, based on guided rails, has been designed for the transport of the boxes. This implement has the size of the most unfavorable standardized box that can be used in the area and is supported on the base of the structure where the set of ultrasound sensors for detecting nearby obstacles is placed. Finally, it has a multilevel rear mast where it carries a camera for people detection, which height can be adjusted depending on the needs of the task.
Publications
- López-Gázquez, A., Mañas- Álvarez, F. J., Moreno, J. C., Cañadas-Aránega, F., Sánchez, J. A., October 22–27 2023. Navigation of a differential robot for transporting tasks in mediterranean greenhouses. Proceedings of the 2023 International Symposium on New Technologies for Sustainable Greenhouse Systems (Greensys). ISHS (International Society for Horticultural Science), Cancún, Mexico, pp. 1–8.
- Moreno Úbeda, J. C., Cañadas-Aránega, F., Rodríguez, F., Sánchez-Hermosilla, J., & Giménez, A. (2022). Modelado 3D y diseño de un robot colaborativo para tareas de transporte en invernaderos. In XLIII Jornadas de Automática (pp. 785-791). Universidade da Coruña. Servizo de Publicacións. [link]
Images and videos

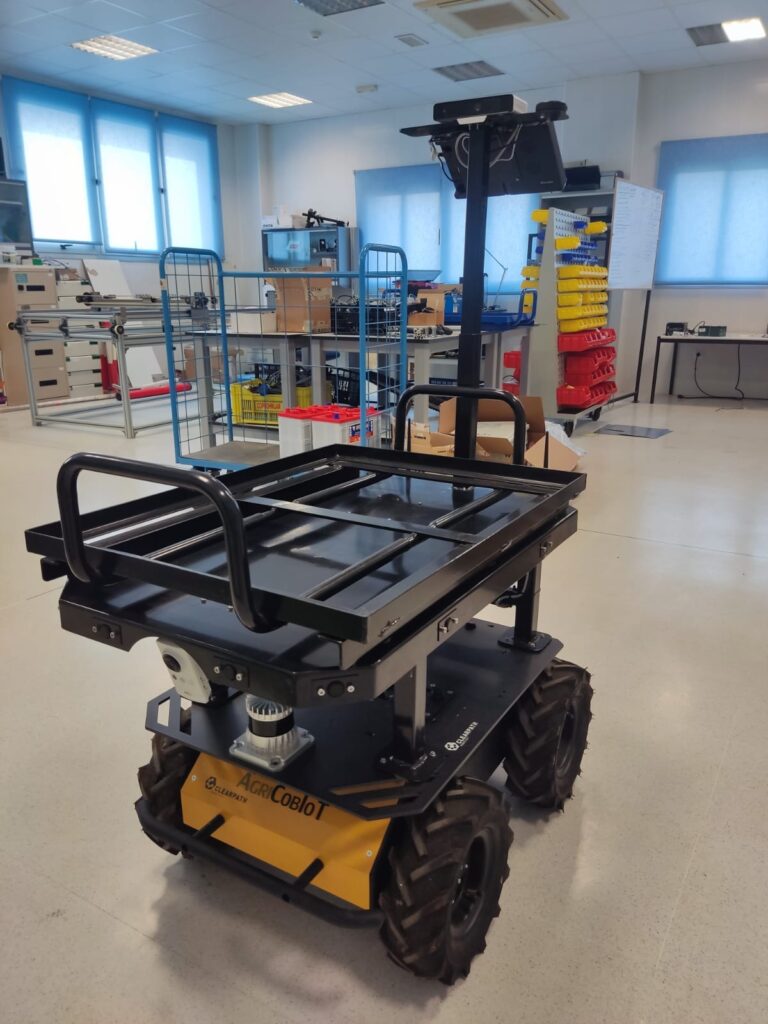
AgriCobIoT II
Description
It is a robot with an Ackermnann structure that allows turns with a 2 m radius. The robot has been specifically designed for transporting boxes and tools inside the greenhouse, with a platform on the upper part with dimensions adapted to the boxes used by farmers in greenhouses in the area. The robot consists of a structure that forms the skeleton of the machine. It has, on the one hand, two forks attached to the chassis which, in turn, are attached to a motor to establish the direction of the robot and, on the other, two bearings connected by an axle to two wheels driven by a traction motor. On the sides there are two protective plates bearing the logos of the project that finances it and, at the front and rear, two bumpers made of rigid PVC are installed. As a novelty, this robot has an extendable mast attached to the rear bumper, where a series of sensors are installed so that it can navigate through the greenhouse (and even outdoors, for example to navigate to an outdoor recharging station or to another greenhouse) and collaborate with human operators.
Publications
- Cañadas-Aránega, F., Moreno, J. C., Blanco-Claraco, J. L., Giménez, A., Rodríguez, F., & Sánchez-Hermosilla, J. (2024). Autonomous collaborative mobile robot for greenhouses: Design, development, and validation tests. Smart Agricultural Technology, 100606. [link]
- Cañadas-Aránega, F., Moreno, J. C., & Blanco-Claraco, J. L. (2024). A PID-based control architecture for mobile robot path planning in greenhouses. IFAC-PapersOnLine, 58(7), 503-508. [link]
- Cañadas-Aránega, F., & Blanco-Claraco, J. L. , Alvarez, F. J. M., & Úbeda, J. C. M. (2024). Navegación de un robot Ackermann para tareas de transporte en invernaderos mediterráneos con MultiVehicle Simulator (MVSim). Jornadas de Automática, (45). [link]
- Cañadas-Aránega, F., Blanco-Claraco, J. L., Moreno, J. C., & Rodriguez-Diaz, F. (2024). Multimodal Mobile Robotic Dataset for a Typical Mediterranean Greenhouse: The GREENBOT Dataset. Sensors, 24(6), 1874. [link]
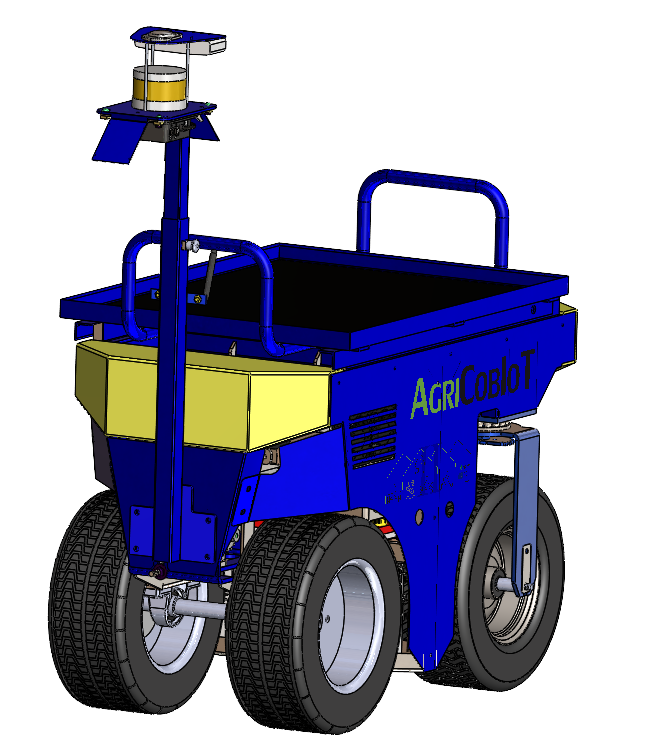
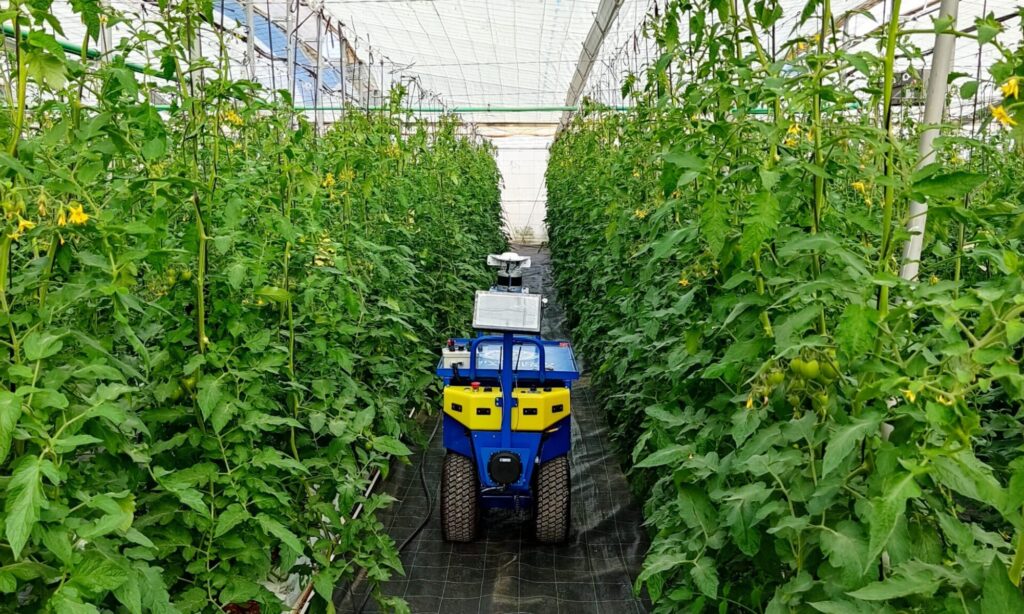
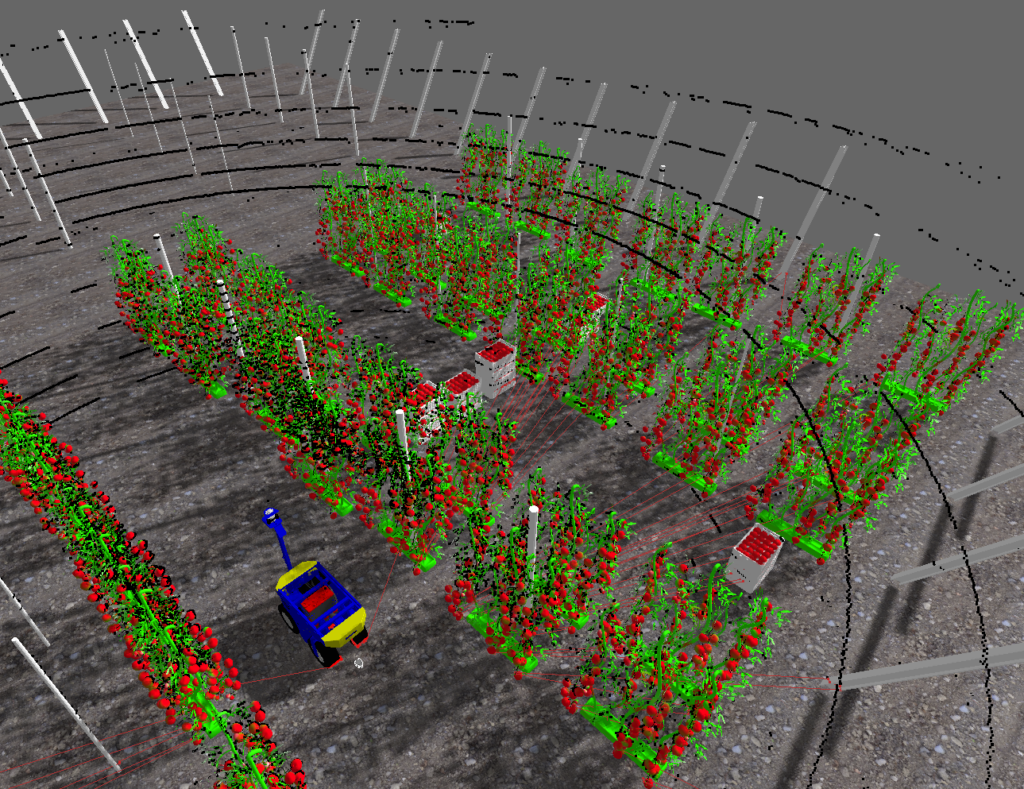